Environment
Operational efficiency and circular thinking have always been a part of the Royal Unibrew’s DNA. Optimizing resource consumption by reducing, reusing and recycling is relevant for all materials, including energy, water and waste (residuals from brewing) both at our production sites but also very importantly in other parts of our value chain such as raw materials, malting, packaging and distribution.
Several projects were implemented in 2019 and many will follow in 2020 and beyond. More information is available in “Future proofing Royal Unibrew”.
Royal Unibrew’s efficiency on energy per produced volume has improved by 12% compared to 2015 irrespective of the acquisitions in 2018 and 2019. The performance on water consumption has also improved, however, the effect of the recent acquisitions was more significant on our water efficiency than on our energy efficiency. Between 2018 and 2019, the energy and water consumption per hl increased slightly.
Royal Unibrew’s production facilities are not located in water scarce areas, but as energy efficiency also is driven by water being pumped from the source to the point of consumption reducing water and energy consumption remains a priority to us. Wastewater is never discharged without treatment.
Well-functioning deposit return systems (DRS) are in place in Denmark, Finland and Lithuania. Similar systems are currently being discussed in France, Latvia and Italy. In the Danish deposit return system, at least 9 out of 10 glass bottles, PET bottles and cans are collected and in Finland, the return system rate is even higher. The deposit return systems are continuosly improved to increase the recyckling rates further. Thus, to ensure availability of recycled packaging material, the Danish DRS is working towards establishing a closed loop food grade recycling system where the materials may be either reused or recycled for food packaging material.
Furthermore, in many of our markets, infrastructure for recycling of material is provided by the local governments, supporting additional collection of material for recycling. The EU waste directive and the extended producer responsibility will enhance this as well. In fact, access to recycled food grade PET will be highly dependent on governments’ ability to deliver on the infrastructure, where deposit return systems are not yet available.
Targets for 2020
- Packaging material (minimum level – average)
-
- >50% recycled paper labels per unit
- >70% recycled carton/corrugated cardboard per volume
- >15% recycled PET per volume
- Test of electricity-based transportation vehicles: Trucks, cars and vans, forklifts, etc.
- 15% CO2 reduction (Green House Gas Protocol, Scope 1 and 2) per hl compared to 2015
- Reduction of potential packaging waste in Americas, Africa and Asia
- Reduce plastic usage
Targets for 2022
- Packaging material (minimum level – average)
- >90% recycled paper labels per unit
- >90% recycled carton/corrugated cardboard per volume
- >30% recycled PET per volume
- Implementation of prioritized electricity-based transportation vehicles
- 30% CO2 reduction (Green House Gas Protocol, Scope 1 and 2) per hl compared to 2015
- Reduce potential packaging waste in Americas, Africa and Asia
- Documented reduction
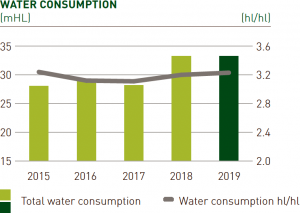
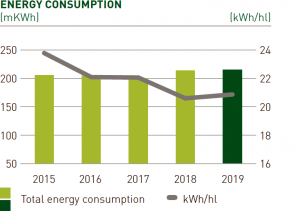
Carbon footprint and renewables
We are well-aware, that the brewing industry’s main CO2 footprint is outside the facilities. When we look at industry averages, the brewing/filling, production and recycling of packaging material as well as distribution account for approximately 75% of the total carbon footprint of our products, where raw material and sales refrigeration contributes the rest.
With reference to the Green House Gas Protocol (GHG), we are confident that the calculated production footprint corresponding to the GHG protocol’s scope 1 and 2 (direct emissions from our activities and indirect emissions from electricity purchased) as it is directly calculated from our energy consumption. Regarding Scope 3 emissions (all other indirect emissions) from sources we do not own or control – in this case packaging material and distribution – we have used industry standards for our initial calculation of the CO2 impact. Other significant Scope 3 contributors such as raw material, including malting and sales refrigeration will be established in the coming years.
For 2019, the initial calculation of the CO2 impact from production, packaging material and distribution was 40, 143, 30 million kg CO2, respectively.
The carbon footprint for our production was reduced by 10%, measured as kg CO2 per produced volume, from the base year 2015 to 2019. Between 2018 and 2019, the kg CO2 per produced volume increased slightly.
Emissions throughout the life cycle
Proportion of greenhouse gas emissions in each stage of the life cycle of our products.
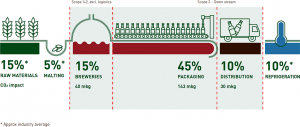
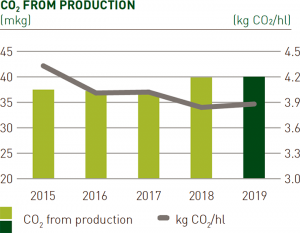
Examples of CO2 dilemmas
- Smaller pack sixes produce more CO₂ per unit
- Move from plastic to glass bottles result in more CO₂
- Producing beer with 0.0% alcohol creates more CO₂ because of a more sophisticated production process
Royal Unibrew is working on investing in renewable energy as a mean to reduce our carbon footprint. In 2020, we will continue the journey of becoming carbon neutral by reducing our Danish, Baltic, Finnish and Italian footprint of electricity consumption via purchase of “green” electricity, corresponding to more than 99% of our consumption. In parallel, we will continue to explore and decide on our investment approach as to renewable energy.
At the same time, Royal Unibrew is working on reducing the impact from packaging material by reducing weight (down weighing) and changing from virgin material to recycled material on e.g. PET and cardboard. In 2019, we introduced recycled: paper labels, corrugated trays and shrink film for several brands.
Our target in the Danish production is a recycled PET fraction of at least 50% on average of our PET bottles in 2021. We have increased the fraction of recycled material steadily in 2019 and our Egekilde Still is now in a 100% recycled PET bottle. Thus, we expect the overall Danish target to be met already in 2020.
Royal Unibrew has been carbon neutral on the Egekilde products for several years based on externally verified CO2 calculations and CO2 credits. We are now applying the environmental life cycle assessment (LCA) methodology for selected materials and categories, among others plastic cups used for events, to meet consumer demands and provide our customers with environmental data for making an informed choice.
Replacement of older distribution vehicles is ongoing in Denmark where we own the distribution vehicles, and likewise, we are looking into electrification of transportation equipment and vehicles at all sites. Increasing the use of renewable energy beyond the national grid mixes is also in the pipeline for 2020. Furthermore, we plan to install charging stations at our headquarter in 2020.
“We continuously strive to identify new measures to reduce our carbon footprint. Therefore, optimizing resource consumption by reducing, reusing and recycling is relevant both at our production sites and in other parts of our value chain such as raw materials, malting, packaging and distribution.”
Future proofing Royal Unibrew
Royal Unibrew strives for continuous improvement. In 2019, we initiated smaller and larger projects at all our production sites.
Water is our most important raw material. Water preservation and water quality therefore remains a key priority, which is why we are extra careful with regard to our wastewater discharge. All our wastewater is treated before emission either at our site or at the municipal treatment plant to meet the requirements. At Lorina in France we have invested in the existing wastewater treatment plant on site to further improve the efficiency. The water is emitted via an on-site aquarium with fish to a small creek outside the facility. The aquarium is more than just a gimmick, as it reminds us of the importance of clean water and help us to make sure that the treatment plant is running optimally.
At our production site in Lahti, Finland, we joined forces with the Lake Vesijarvi Foundation in 2019 to protect the lake and to promote all efforts to improve its water quality. Lake Vesijarvi’s wellbeing affects a large ecosystem in the Lahti area. Together with local restaurants, we released more than 2,000 trouts and pikeperches into the lake aiming to restore the eco system. In 2020, the collaboration will be expanded even further.
At several of our sites in the Baltics and Denmark, we have implemented improvements to our cooling/heating systems. For example, cooling systems are upgraded to more energy efficient systems from temporary and decentralized cooling facilities to centralized permanent systems. Many projects will be continued in 2020 and beyond.